BACKGROUND
In preparation for the new High Speed 2 (HS2) railway Phase 1 link to the West Midlands and future Phase 2B extension to Leeds, Rayden Engineering Ltd (REL) were contracted by Valero to divert their existing 300NB (12”) High Pressure (HP) multi-product pipeline running between Seisdon and Kingsbury in Warwickshire.
This welded steel pipeline is managed by Mainline Pipelines Limited (MPL), a division of Valero that takes care of their UK cross-country pipeline network. The existing pipeline was built in 1973, on what was then agricultural land, prior to construction of the Kingsbury section of the M42 motorway between Junctions 9 / 10 (completed 1985).
The pipeline ran parallel to the Birmingham & Fazeley Canal before crossing a Cadent gas pipeline and then the canal by pipe bridge. Continuing Northeast the pipeline then crossed under the M42 motorway north of Junction 9, near Marston Lane Bridge, before travelling east towards Kingsbury.
The HS2 Phase 1 West Midlands link runs parallel to the M42 and crosses the existing pipeline and carriageway east of Marston Lane. The proposed Phase 2B line to Leeds will run alongside this to the east, also crossing the pipeline. This route continues north, on the eastern side parallel to the southbound carriageway of the M42
To enable this, substantial HS2 infrastructure works were required including the demolition of the existing Marston Bridge which was directly above the pipeline. Works also included construction of the new Marston Box Rail Bridge to cross the M42 motorway, the UK’s first ‘box-slide’ bridge. This connects Dunton Wood Embankment to the south and to a new Birmingham & Fazeley Canal Viaduct that crosses the canal to the north.
In preparation for HS2 a feasibility study was carried out in 2013. This recommended that the existing pipeline should be diverted in advance of any construction works to maintain its safety and integrity.
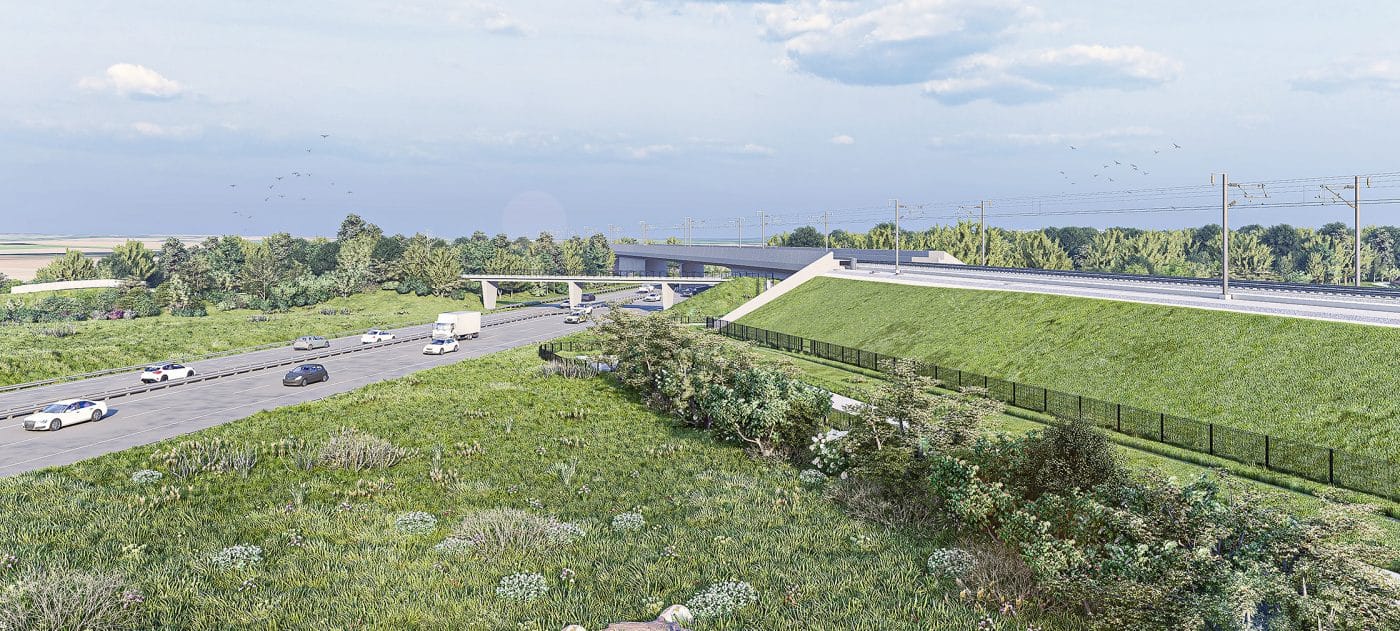
ABOUT VALERO
Valero is the world’s largest independent petroleum refiner and producer of renewable fuels. In the UK and Ireland, the company markets fuels under the Texaco brand through a network of around 750 (UK) and 230 (Ireland) Texaco service stations.
Valero also own and operate the Pembroke Refinery in southwest Wales, which is one of Europe’s largest and most complex refineries. This processes crude oils into gasoline, diesel, jet fuel, heating oil, and low-sulphur fuel oil.
In the UK, Valero also has ownership interests in four major pipelines, nine fuel terminals and a 14,000-barrel-per-day aviation fuels business. The company supplies fuel products to its UK customers via its fuel terminals and pipelines.
Plan of pipeline diversion route
SCOPE
REL were employed directly by MPL and appointed as Principal Designer/Contractor, under CDM (Construction Design & Management) 2015. This meant REL were fully responsible for the complete design and build of the project.
Initial scope consisted of the design, supply, construction, and commissioning of:
- New route for existing 300NB (12”) HP pipeline at Marston Lane Bridge for HS2 diversion.
- Trenchless crossing of M42 motorway, Birmingham & Fazeley Canal & existing Cadent pipeline.
- Design & build of two new valve compounds each end of diversion (Marston Lane & Lichfield) to isolate pipeline for maintenance & repair.
- Tie-in of both ends of newly diverted section to existing pipeline.
- Completion of all pipework modifications & associated civil works throughout.
- Testing & commission of new pipeline section.
- Decommissioning & removal of any redundant pipework.
A key requirement was to ensure that safety and integrity of the existing pipeline remained intact, and that construction caused minimal impact to landowners, the local community, public highways & Byways, the canal, wildlife, and the environment as a whole.
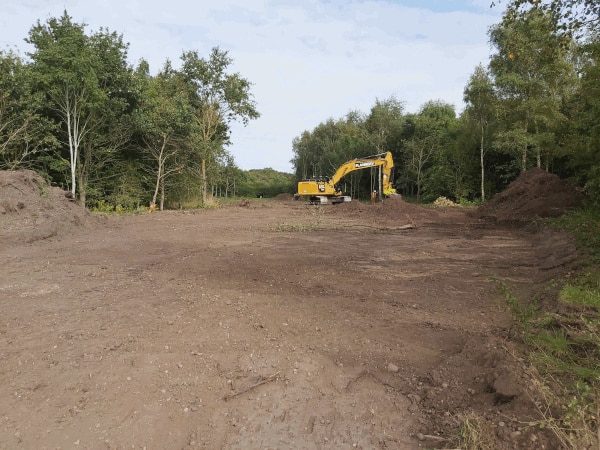
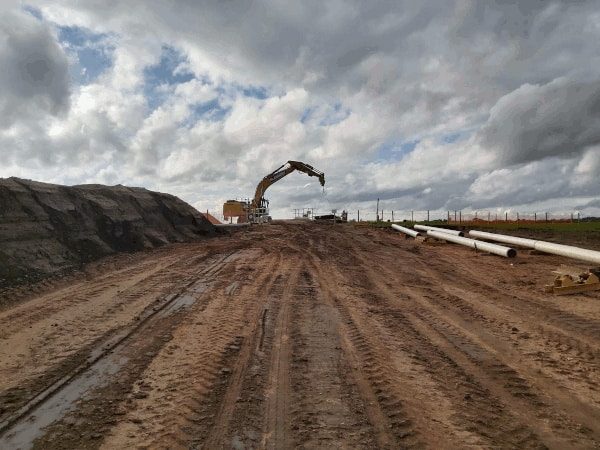
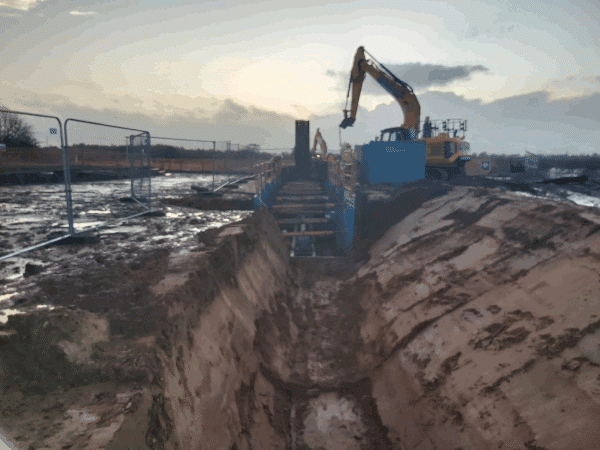
SERVICES DELIVERED
The contract was delivered on a turnkey basis with full responsibility for all aspects of work from initial engineering and design; to procurement, fabrication, and construction; through to reinstatement, final as-built handover, and project aftercare.
Design & Planning
REL completed the detailed design and planning of all permanent works. All design complied with the HS2 London-West Midlands Act 2017 and requirements of HS2 Non-Contestable Utilities Design & Review Guide.
Design code was in accordance with ASME B31.4: 2016 Pipeline Transportation Systems for Liquids & Slurries and where appropriate incorporating BS PD 8010-1:2015 Pipeline systems. Steel Pipelines on Land.
Temporary works (TW) design was carried out in accordance with BS 5975:2019.
The pipeline diversion was designed and managed to have minimal environmental impact on the surrounding area, particularly at the Southwestern tie-in by Fox’s Bridge where an active badger sett was identified and avoided.
REL worked closely with all stakeholders liaising with required statutory bodies to obtain any approvals, permits and other consents needed for construction.
Once all designs were approved, REL mobilised to site for commencement of the construction stage.
Pipeline Route & Specification
The developed diversion route was largely determined during the initial phase of the project based on the feasibility study, position of current and future HS2 railway lines and any legislative factors effecting location.
Design calculations recommended a 300NB (12”) pipeline, of welded steel grade API 5L PSL 2 X52 with wall thickness 9.5mm (open cut) or 14.3mm (crossings); 96.2 barg pressure.
The diversion route included two special crossings.
Crossing 1 was a HDD crossing underneath Marston Lane; the M42 motorway; the new HS2 rail connection to the West Midlands; the proposed HS2 Phase 2B route to Leeds; and the Birmingham & Fazeley Canal.
Crossing 2 was a service crossing for an existing 300NB Cadent HP gas pipeline.
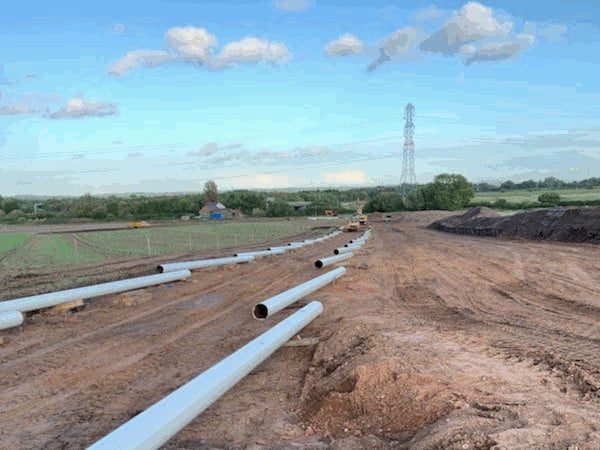

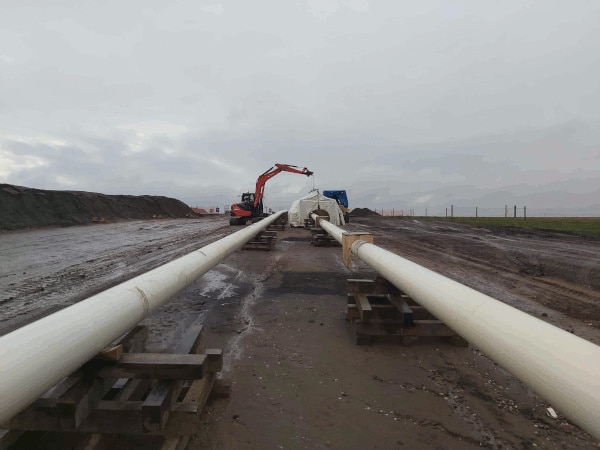
The following works were completed during pipeline construction:
- Ground penetrating radar (GPR), geotechnical, ecology, environmental & topography survey & reporting to manage obstructions & any wildlife / environmental factors effecting route.
- Site preparation, setting out, clearing, stripping of topsoil, temporary fencing, installation of hardstanding area & site welfare facilities.
- New steel 300NB (12”) pipeline was installed using open cut & trenchless methods.
- REL completed all civils & any associated works needed for the project.
- Pipework buried underground to minimum depth of 1.2m for open cut and 2.5m+ for crossing points to suit construction methods.
- Excavation of open cut sections & pits for Northeast & Southwest tie-ins sites.
- All pipework, fittings & accessories were provided free issue by Valero. This was collected by REL from the Kingsbury depot.
- All handling, transport & storage of pipe was in accordance with IGE/TD/1 Edition 5 Supplement 1 Handling, Transport and Storage of Steel Pipe, Bends & Fittings.
- Stringing of pipe & bends to match existing ground profile for open cut & trenchless crossing methodology, prefill & testing.
- Pipe bending was overseen by REL engineer as per bending schedule. 19 cold bends were completed complying to ASME B31.4 section 404.2.
- Line up of pipeline completed ready for field welding.
- All welds were numbered & in accordance with Specification Field Welding of Steel Pipelines and Installations, ASME B 31.4, alongside AP STD 1104 & API 11-5.
- Non-Destructive Testing (NDT) completed using phased array plus visual examination, any weld defects were remedied by a repair welder & re-inspected.
- All pipework in field, welds & joints coated with 2-part epoxy, in accordance with SP 2888
- Field joints & tie-ins coated with STOPAQ CZ wrap, with a layer of STOPAQ Outer wrap.
- All coatings tested to NACE SP0490, NACE RP0105 & NACE RP0394.
- Controlled lower laying & tie-in of open cut sections.
- Pipe laid on a 150mm thick fine graded sand bed & carefully compacted with another 150mm thick layer on top.
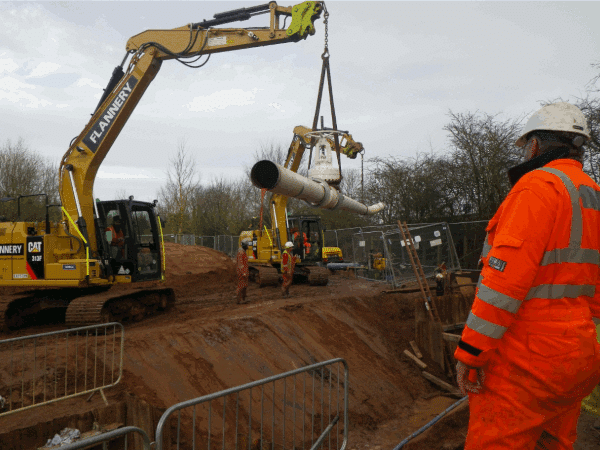
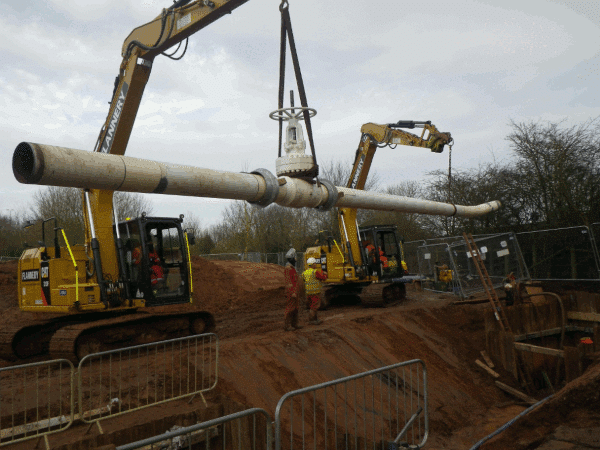
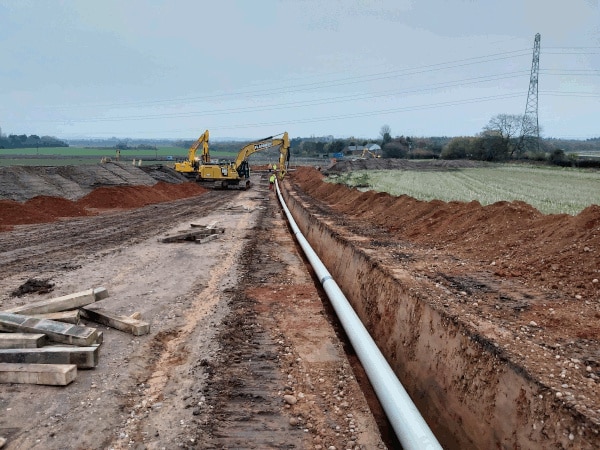
19. Design & Build of Two Valve Access Compounds
- Compounds were built to isolate the new pipeline for maintenance & repair purposes. Each was located either end of diversion near new tie-in points – one at Marston Lane & the other at Lichfield Road.
- Work included all civils & pipework.
- Completed ground preparation & excavation for construction of two 3.5m × 3.5m concrete compounds 2.4 or 2.8m deep with 250mm thick reinforced walls.
- The internal chamber included a drainage sump & concrete support for the isolation valve which was cast into the base. Puddle flanges & link seals were used on pipework entering the wall to prevent any water ingress into pit.
- REL also fabricated & installed a galvanised steel ladder & standing platform to facilitate safe access to the pit & valve operation.
- To prevent unauthorised access & debris entering the pit a lockable multi-leaf steel security cover was fitted. This consisted of 7 covers weighing 50kg.
- On the outside, the compound was surrounded by a 6.3m x 6.3m x 2.5m high Barbican Security fence & gate. A new access path 110m – 130m long with new pedestrian access gate (Lichfield Road only) was also constructed.
- Decommissioning & tie-in was completed same time as main diversion tie-ins.
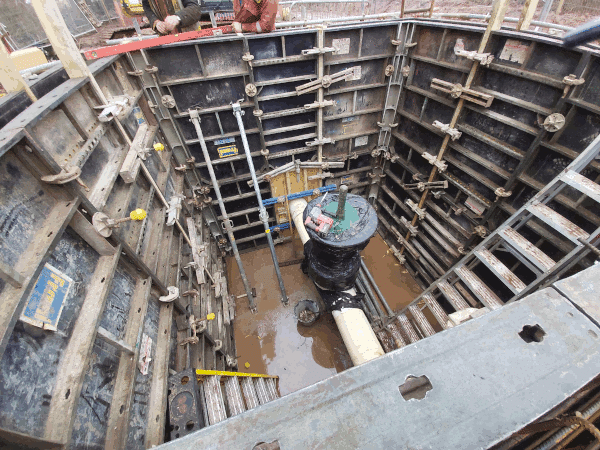
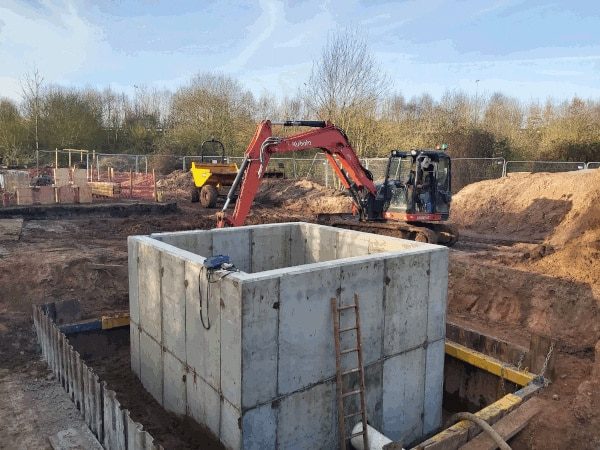
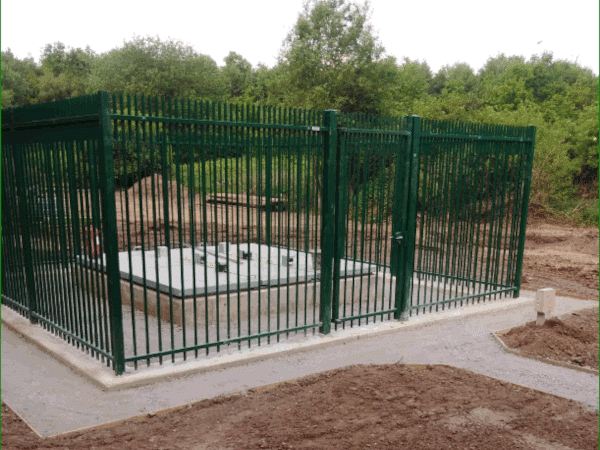
20. Crossing 1 – Central Section of New Pipeline
- This crossed from East to West underneath Marston Lane; M42; both new HS2 routes; & the canal. REL utilised a Horizontal Directional Drilling (HDD) technique which was the most effective & least disruptive solution.
- Starting just East of Marston Lane, a temporary pit was excavated to receive the HDD machine.
- A 450mm bore hole was drilled following a guided route that arced under the landscape above. Entering at an angle of 15o & 2.2m below ground level, the bore hole reached a depth of 28-30m before flattening off & then ascending to reach ground level just West of Birmingham & Fazeley Canal.
- The fabricated pipework was then laid out above ground & pulled back through the 450mm bore hole using the pre-attached REL fabricated pulling head. Pipe was pulled through in a controlled manner until its full length had been installed.
- The void between the 300mm pipe & the 450mm bore hole was filled with Bentonite Grout.
- The HDD methodology enabled a continuous section of underground pipe to be installed spanning a total length of 605m with only its two end points exposed.
- All work complied with Canal & Rivers Trust, Highways England & HS2 requirements.
21. Crossing 2 – Cadent Pipeline
- Due to its age & issues on the Cadent gas network, their pipeline was classified as high-risk T/PM/P/18. This meant it could not be exposed through open cut, therefore REL opted for an auger bore trenchless crossing method which was the safest & most efficient solution.
- Two temporary pits were excavated either side of the Cadent pipeline. A 3.3m x 16m drive pit for the auger bore drilling machine & a reception pit 2.3m x 4m, both to a depth of just under 4m’s. To facilitate this TWs also included access steps, fencing, hard standing, sheet piling & a slit trench to monitor depth of cover.
- The auger bore was then set on a course towards the reception pit cutting a bore hole 12m long at a depth of 3.2m – 1.5m below the Cadent pipeline. The fabricated pipework was set out above & threaded through the hole before tie-in of both exposed ends.
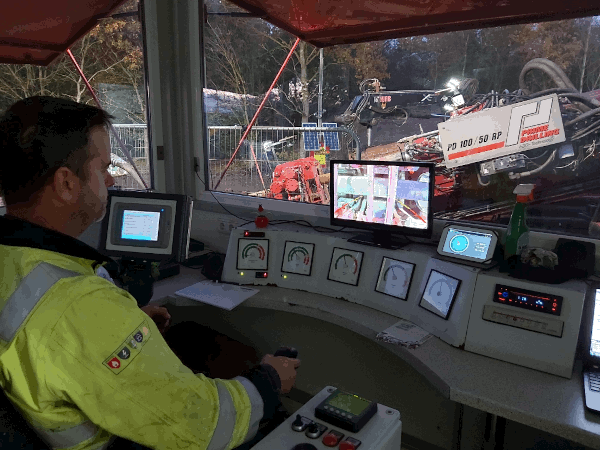
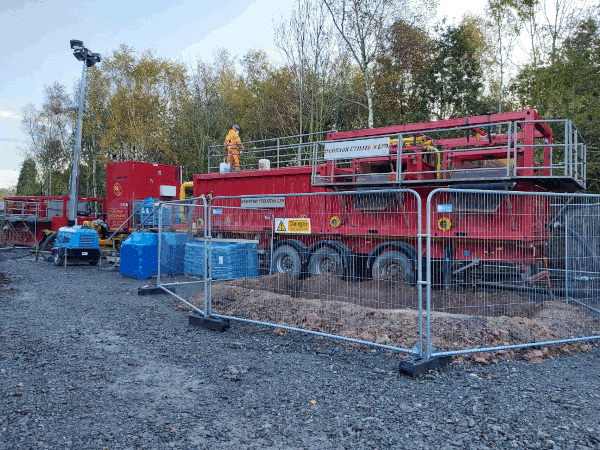

- Cold cut Tie-ins completed at both ends of new pipework section southwest of Fox’s bridge & northeast of Marston Lane to connect to existing Seisdon & Kingsbury pipeline. This included purging the line, cutting old pipe section, welding new section to existing, inspection, testing & recommissioning. Pipeline was decommissioned for a 5-day when all tie-work was completed.
- Backfilling & compacting of all exposed pipework, including access chambers. Where possible any flooded trenches were drained & original soil used.
- Pipeline tested for high level hydrostatic strength, pneumatic strength & leak testing to API 1110 – Pressure Testing of Steel Pipelines, to demonstrate fitness for purpose. Water for tests was extracted from Birmingham and Fazeley canal.
- All pipeline sections dried to dew point of -20°C to ensure no water was present that could lead to corrosion prior to commissioning of the pipeline.
- Pipeline recommissioning to ASME B31.4 – Pipeline Transportation Systems for Liquid Hydrocarbons & Other Liquids.
- Pipeline tied into existing Cathodic Protection system with 4 new test posts installed.
- Any redundant pipework, above & below ground, where possible was excavated & removed such as crossing at Foxes bridge & tie-in locations.
- Any redundant pipework, not removed, was grouted with foam concrete or similar cementitious grout to prevent future collapse.
- Once all phases of work were complete hardstanding areas, bog mats & Heras fencing, were removed.
- Topsoil was graded, replaced & reseeded.
- Landscape was reinstated to an equivalent standard – to the satisfaction of MLP, HS2 & North Warwickshire Borough Council requirements – including all working areas & access.
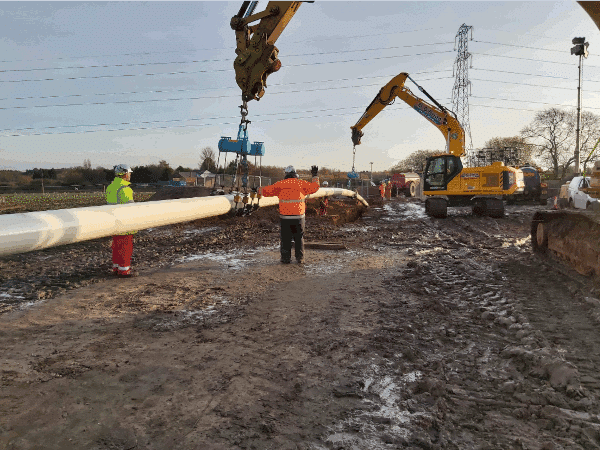
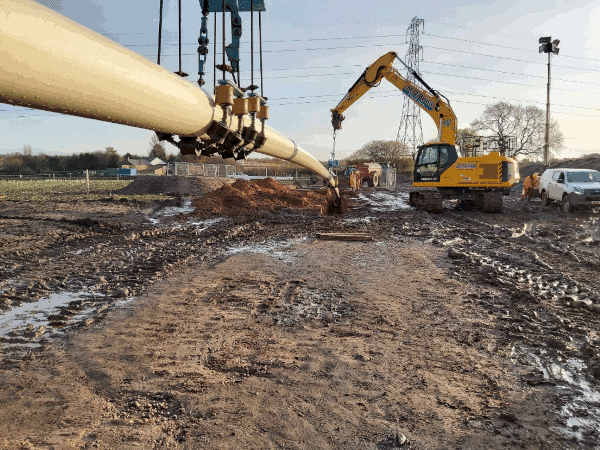
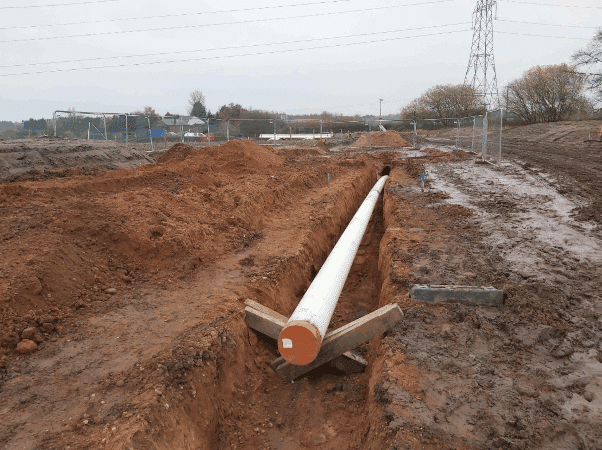
To support delivery of this project REL also:
- Implemented the REL integrated project management system to ensure efficient planning, design & construction & full collaboration between stakeholders throughout the project lifecycle. REL adopted Building Information Modelling (BIM) technologies & processes in line with current British Standards and Codes of Practice.
- Set-up dedicated project management team covering: Detailed Design & Engineering, Material Procurement, Construction, HS&E, Quality, Planning & Progress. Included key site-based staff & office-based REL personnel.
- Monitored project & kept it on track with monthly meetings for: progress updates; quality, traffic liaison; & technical working groups along with a quarterly financial meeting. These were supported with additional reporting.
- Managed & controlled detailed documentation to meet approval needs of CDM & other regulatory bodies. This included: : Contract & Works Programme; Procurement Plan; Health, Safety, Environmental & Quality Plans; RAMS; Risk Register; Construction Logistics Plan; Traffic Management Plan; Works Procedures (Weld, Painting, NDT, etc.); Temporary Works Designs, Final Designs & Construction Issue Drawings, HS2 Verification & Validation Matrix, Construction & Commitment Compliance Plans.
- Provided any other services as needed to enable completion of works.
- Waste management for site complying to HS2 Environmental Minimum Requirements (EMR).
- Site access control, security & traffic management.

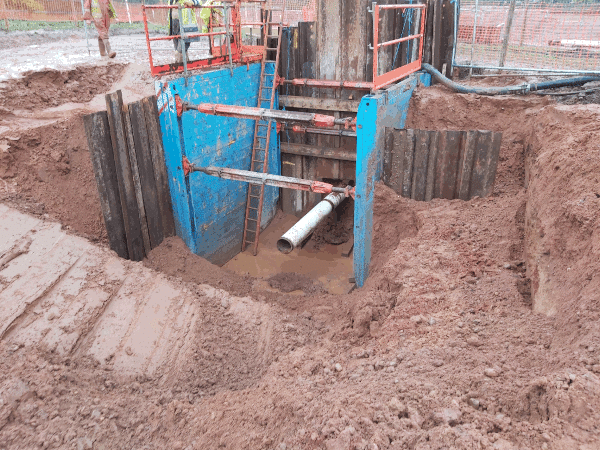
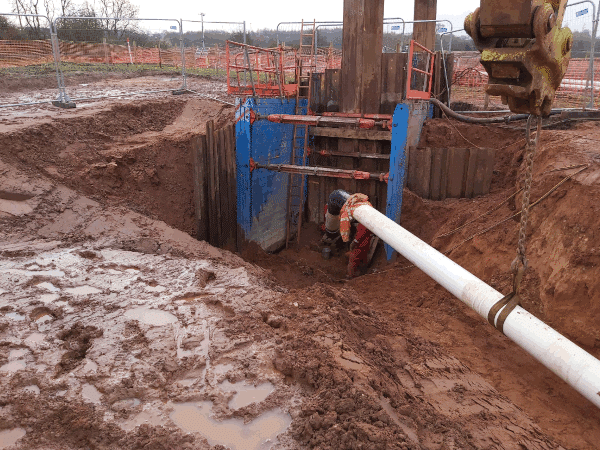
OUTCOME
The project took 14 months, including all design and construction works, and was completed May 2020. On handover REL provided full ‘As Built Drawings’ for all works completed.
The project was delivered in line with approved designs, programme specifications, within budget and without any major issues. REL fully satisfied their duties under CDM 2015 and met all compliance / approvals needs for HS2 and Valero – MPL, the client.
The trenchless construction techniques – HDD & auger bore – used for crossing the Cadent pipeline, the M42, canal and rail crossings provided many benefits as opposed to traditional open cut methods. It meant work was completed very quickly, safely and in all weathers – without disturbing the ground above. This caused minimal disruption to car, rail, and boat traffic flow above, a low carbon footprint with much less impact on the local community, environment, and wildlife.
As part of the contract aftercare, monitoring and management was provided for a period of one year following completion of all works. This was extended to three years for any works beneath the Birmingham and Fazeley Canal.
Throughout this period REL rectified any remedial works identified. An annual report was provided (on each anniversary of completion) detailing performance of the environmental design, installed mitigation measures and results of any monitoring undertaken over the period.
At the end of the 3-year aftercare period REL compiled a post-commissioning evaluation report to satisfy the client that key objectives and deliverables were achieved, as agreed at the start of the project.

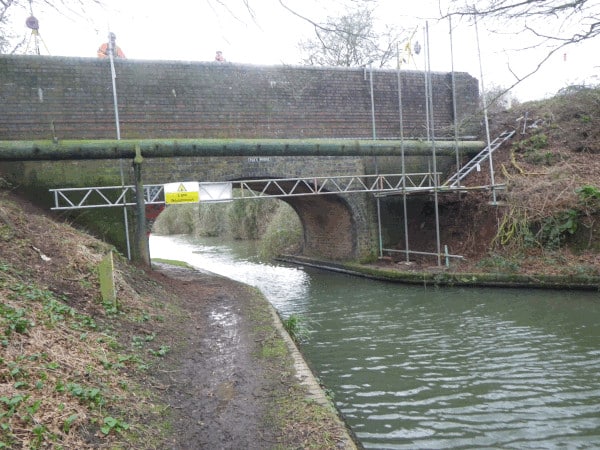
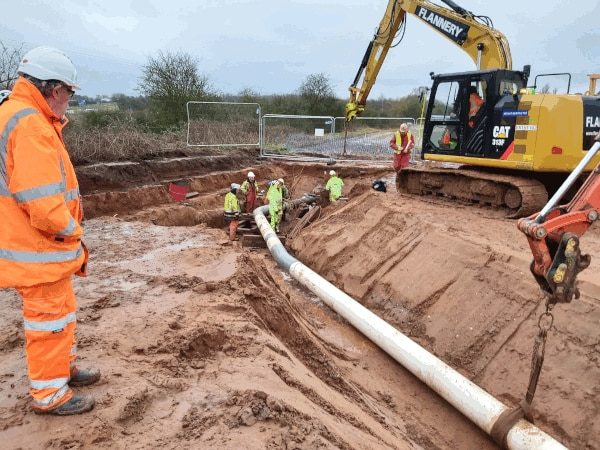